簡介
由于ABS不導(dǎo)電,因此無法在其表面直接電鍍金屬合金,abs塑料在經(jīng)過粗化敏化還原,解膠加速話等工序后,將在制品的表面形成一層貴金屬膜。從而加速化學(xué)鍍的還原反應(yīng)。使度化反應(yīng)更加順利的進(jìn)行。
ABS塑料電鍍問題的原因分析和解決方法
燈罩電鍍后表面出現(xiàn)黑斑,無光澤燈罩化學(xué)鍍銅后,轉(zhuǎn)入電鍍工序,我們采用的工藝流程是:鍍鎳→鍍銅→鍍亮鎳→鍍鉻。鍍銅溶液比較穩(wěn)定,主要問題是銅陽極在電鍍中易產(chǎn)生銅粉(Cu2O),銅粉進(jìn)入鍍液會引起鍍層粗糙。我們用耐蝕性陽極布包住陽極再放入陽極套中,電鍍后經(jīng)常打開清洗,因此,鍍銅后表面光亮、細(xì)致、沒出現(xiàn)任何問題。零件鍍亮鎳后表面無光澤,而且有黑斑,加光亮劑后,問題仍未消除,分析槽液,各成分含量均在范圍之內(nèi)。槽液放置一夜后,把上清液全部倒到備用槽,發(fā)現(xiàn)鍍槽底部有黃褐色泥狀沉淀物。經(jīng)分析是由于鍍鎳溶液溫度偏高,光亮劑分解所致,電鍍時(shí),空氣攪拌裝置把槽底的泥渣翻起來,同鎳離子一起沉積到鍍層上,造成毛刺和黑斑。后來還發(fā)現(xiàn),由于鍍鎳、鍍鉻同用一套導(dǎo)電棒,導(dǎo)電棒上帶有鍍鉻時(shí)留下的鉻酐,鍍鎳時(shí),易將鉻帶入鎳槽中;又由于掛具沒有絕緣,鍍鎳溶液中帶入了銅雜質(zhì),這些都是引起發(fā)黑的原因。銅雜質(zhì)可用0.5A/dm2電流密度電解除去。去除六價(jià)鉻,先用硫酸調(diào)節(jié)鍍液pH至3左右,然后加入亞硫酸鈉0.2~0.4g/L,攪拌,使六價(jià)鉻還原為三價(jià)鉻,然后用低電流密度除去三價(jià)鉻。最后用活性炭處理過濾除去有機(jī)雜質(zhì)。槽液經(jīng)處理后,鍍鎳后再沒有出現(xiàn)黑斑。套鉻時(shí),燈罩的凹部采用象形陽極,最后鍍出的燈罩光亮、細(xì)致,符合產(chǎn)品要求。塑料件的成分及成型工藝不能忽視,這往往是電鍍工作者不易覺察的問題。電鍍時(shí)要設(shè)計(jì)專用的掛具。注意槽液的維護(hù),使各成分保持在工藝規(guī)范內(nèi)。加強(qiáng)工序間的清洗,不要把其它雜質(zhì)帶入。
基本概念
目的abs電鍍的目的是將塑料表面披覆上金屬,不但增加美觀,且補(bǔ)償塑料的缺點(diǎn),賦予金屬的性質(zhì),充分發(fā)揮塑料及金屬的特性于一體,已有大量塑料電鍍產(chǎn)品應(yīng)用在電子、汽車、家庭用品等工業(yè)上。
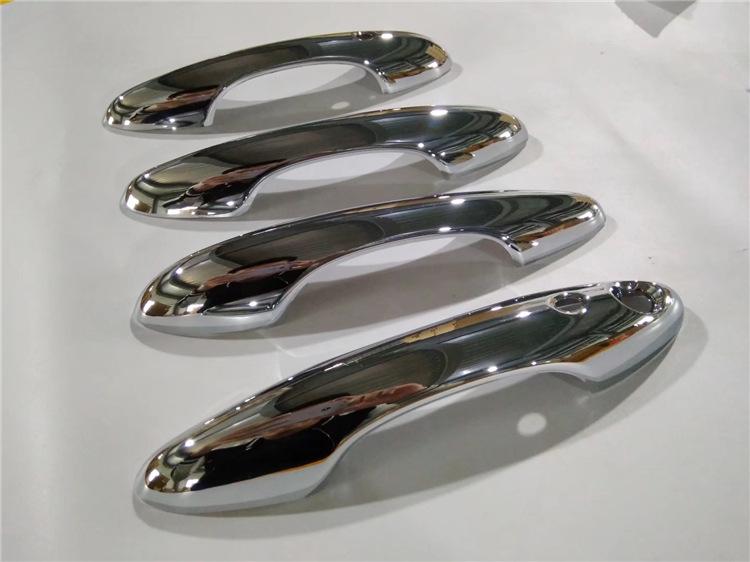
abs電鍍
過程(1)清潔(cleaning):去除塑料成型過程中留下的污物及指紋,可用堿劑洗凈再用酸浸中和及水洗干凈。
(2)溶劑處理(solvent treatment):使塑料表面能濕潤(wetting)以便與下一步驟的調(diào)節(jié)劑(conditioner)作用。
(3)調(diào)節(jié)處理(conditioning):將塑料表面粗化成內(nèi)鎖的凹洞以使鍍層密著住不易剝離,也稱為化學(xué)粗化。
(4)敏感化(sensitization):將還原劑吸附在表面,常用(stannous chloride)或其它錫化合物,就是sn離子吸附于塑料表面具有還原性表面。[1]
隨著工業(yè)的迅速發(fā)展、塑料電鍍的應(yīng)用日益廣泛,成為塑料產(chǎn)品中表面裝飾的重要手段之一.國內(nèi)外已廣泛在ABS、聚丙烯、聚砜、聚碳酸酯、尼龍、酚醛玻璃纖維增強(qiáng)塑料、聚苯乙烯等塑料表面上進(jìn)行電鍍,其中尤以ABS塑料電鍍應(yīng)用最廣,電鍍效果最好。
塑料電鍍(plastic plating)的優(yōu)點(diǎn):
1.成型容易、成形好。
2.重量輕。
3.耐蝕性佳。
4.耐藥性好。
5.電絕緣性優(yōu)良。
6.價(jià)格低廉。
7.可大量生產(chǎn)。
缺點(diǎn):
1.耐候性差、易受光線照射而脆化。
2.耐熱性不好。
3.機(jī)械強(qiáng)度小。
4.耐磨性很差。
5.吸水率高。
影響因素
注射機(jī)選用注射機(jī)選用不當(dāng),有時(shí)會因?yàn)閴毫^高、噴嘴結(jié)構(gòu)不合適或混料使制件產(chǎn)生較大的內(nèi)應(yīng)力,從而影響鍍層的結(jié)合力。
塑件選材塑料的種類很多,但并非所有的塑料都可以電鍍。有的塑料與金屬層的結(jié)合力很差,沒有實(shí)用價(jià)值;有些塑料與金屬鍍層的某些物理性質(zhì)如膨脹系數(shù)相差過大,在高溫差環(huán)境中難以保證其使用性能。用于電鍍最多的是ABS,其次是PP。另外PSF、PC、PTFE等也有成功電鍍的方法,但難度較大。
塑件造型在不影響外觀和使用的前提下,塑件造型設(shè)計(jì)時(shí)應(yīng)盡量滿足如下要求。
(1)金屬光澤會使原有的縮癟變得更明顯,因此要避免制品的壁厚不均勻狀況,以免出現(xiàn)縮癟,而且壁厚要適中,以免壁太薄(小于1.5mm),否則會造成剛性差,在電鍍時(shí)易變形,鍍層結(jié)合力差,使用過程中也易發(fā)生變形而使鍍層脫落。
(2)避免盲孔,否則殘留在盲孔內(nèi)的處理液不易清洗干凈,會造成下道工序污染,從而影響電鍍質(zhì)量。
(3)電鍍工藝有銳邊變厚的現(xiàn)象。電鍍中的銳邊會引起尖端放電,造成邊角鍍層隆起。因此應(yīng)盡量采用圓角過渡,圓角半徑至少0.3mm以上。平板形塑件難電鍍,鍍件的中心部分鍍層薄,越靠邊緣鍍層越厚,整個(gè)鍍層呈不均勻狀態(tài),應(yīng)將平面形改為略帶圓弧面或用桔皮紋制成亞光面。電鍍的表面積越大,中心部位與邊緣的光澤差別也越大,略帶拋物面能改善鍍面光澤的均勻性。
(4)塑件上盡量減少凹槽和突出部位。因?yàn)樵陔婂儠r(shí)深凹部位易露塑,而突出部位易鍍焦。凹槽深度不宜超過槽寬的1/3,底部應(yīng)呈圓弧。有格柵時(shí),孔寬應(yīng)等于梁寬,并小于厚度的1/2。
(5)鍍件上應(yīng)設(shè)計(jì)有足夠的裝掛位置,與掛具的接觸面應(yīng)比金屬件大2~3倍。
(6)塑件的設(shè)計(jì)要使制件在沉陷時(shí)易于脫模,否則強(qiáng)行脫模時(shí)會拉傷或扭傷鍍件表面,或造成塑件內(nèi)應(yīng)力而影響鍍層結(jié)合力。
(7)當(dāng)需要滾花時(shí),滾花方向應(yīng)與脫模方向一致且成直線式.滾花條紋與條紋的距離應(yīng)盡量大一些。
(8)塑件盡量不要用金屬鑲嵌件,否則在鍍前處理時(shí)嵌件易被腐蝕。
(9)塑件表面應(yīng)保證有一定的表面粗糙度。
模具設(shè)計(jì)為了確保塑料鍍件表面無缺陷、無明顯的定向組織結(jié)構(gòu)與內(nèi)應(yīng)力,在設(shè)計(jì)與制造模具時(shí)應(yīng)滿足下面要求。
(1)模具材料不要用鈹青銅合金,宜用高質(zhì)量真空鑄鋼制造,型腔表面應(yīng)沿出模方向拋光到鏡面光亮,不平度小于0.2mm,表面最好鍍硬鉻。
(2)塑件表面如實(shí)反映模腔表面,因此電鍍塑件的模腔應(yīng)十分光潔,模腔表面粗糙度應(yīng)比制件表面表面粗糙度高1~2級。
(3)分型面、熔接線和型芯鑲嵌線不能設(shè)計(jì)在電鍍面上。
(4)澆口應(yīng)設(shè)計(jì)在制件最厚的部位。為防止熔料充填模腔時(shí)冷卻過快,澆口應(yīng)盡量大(約比普通注射模大10%),最好采用圓形截面的澆口和澆道,澆道長度宜短一些。
(5)應(yīng)留有排氣孔,以免在制件表面產(chǎn)生氣絲、氣泡等疵病。
(6)選擇頂出機(jī)構(gòu)時(shí)應(yīng)確保制件順利脫模。
分析
材料分析國際上塑料電鍍在20世紀(jì)50年代已形成規(guī)模生產(chǎn),我國在20世紀(jì)60年代中期也開始進(jìn)行塑料電鍍的生產(chǎn),當(dāng)時(shí)主要用于鈕扣、帶扣等小產(chǎn)品,質(zhì)量要求以不起皮象金屬一樣就可以了。隨著時(shí)代的發(fā)展,產(chǎn)品質(zhì)量的不斷提高,對鍍層質(zhì)量的要求也要相應(yīng)的提高。
在改革開放之前,產(chǎn)品質(zhì)量的提高,是由行政命令下達(dá)指標(biāo)的形式來實(shí)現(xiàn)的,但改革開放后的情況就不同了,“上級”沒有了,指標(biāo)也沒有了,而客戶的要求就成了產(chǎn)品質(zhì)量的指標(biāo),這指標(biāo)你可以達(dá)到,也可以不達(dá)到,然而是關(guān)系到廠家及其工藝的生存或淘汰。
因此,凡提出的質(zhì)量要求都是非常實(shí)質(zhì)性的或是真正有效的,而且在經(jīng)濟(jì)上還要可行的。當(dāng)今塑料電鍍質(zhì)量要求不斷提升的動力在于我國外資企業(yè)的發(fā)展,因?yàn)樵趪H上,尤其是我國的臺灣省和鄰近的日本,都希望利用大陸的現(xiàn)有條件來加工產(chǎn)品,并達(dá)到要求的質(zhì)量水平,這就暴露出我們塑料電鍍質(zhì)量的不足,迫使我們提高質(zhì)量。
塑料電鍍質(zhì)量的現(xiàn)狀:國際上工業(yè)先進(jìn)國家的塑料電鍍質(zhì)量水平確實(shí)很高,在我國廣東地區(qū)有些外資單位鍍件的質(zhì)量水平也是不錯(cuò)的,浙江也有部分單位不差。主要表現(xiàn) 在外觀上能與國外先進(jìn)產(chǎn)品相媲美,并能達(dá)到外資企業(yè)質(zhì)量的要求。至于內(nèi)在質(zhì)量因測試手段和測試的規(guī)范還不健全,質(zhì)量參差不齊。
近年來,塑料電鍍已被廣泛應(yīng)用在塑料零件的裝飾性電鍍上。ABS塑料是塑料電鍍中應(yīng)用最廣的一種。ABS塑料是丙烯腈(A)、丁二烯(B)、苯乙烯(S)的三元共聚物。對電鍍級ABS塑料來說,丁二烯的含量對電鍍影響很大,一般應(yīng)控制在18%~23%。丁二烯含量高,流動性好,易成型,與鍍層附著力好。由于ABS是非導(dǎo)體,所以電鍍前必須附上導(dǎo)電層。形成導(dǎo)電層要經(jīng)過粗化、中和、敏化、活化、化學(xué)鍍等幾個(gè)步驟,比金屬電鍍復(fù)雜,在生產(chǎn)中容易出現(xiàn)問題。我們從塑料電鍍的工藝出發(fā),分析原因并找出了解決的辦法。
1、鍍件易漂浮,與掛具接觸的地方易被燒焦因?yàn)樗芰系谋戎匦。栽谌芤褐幸赘∑?。燈罩外形就象一個(gè)小盤一樣,內(nèi)表面凹進(jìn)去,邊上有兩個(gè)小孔,開始只用一根銅絲卡著兩個(gè)小孔進(jìn)行電鍍。由于電鍍中氣體的放出,燈罩易與銅絲脫離,加之銅絲也輕,不足以使燈罩浸入溶液里。后來在銅絲上附上重物,解決了漂浮問題。銅絲與燈罩的接觸點(diǎn)被燒焦,并露出塑料,是因?qū)щ姴涣家鸬?。為了解決工件漂浮與導(dǎo)電問題,我們設(shè)計(jì)了專門的夾具。夾具有一定的重量,上燈罩后不再浮起,再用兩個(gè)較寬的導(dǎo)電片卡在燈罩的孔上,使各處電流均勻,接觸點(diǎn)就不會燒焦了。
2、燈罩化學(xué)鍍銅時(shí)出現(xiàn)氣泡,電鍍后氣泡變大,并可以揭起塑料電鍍的工藝流程為:除油→水洗→粗化→水洗→敏化→自來水洗→去離子水洗→活化→水洗→化學(xué)鍍銅→水洗→電鍍→水洗→干燥。由以上可知,化學(xué)鍍銅前的任何步驟出現(xiàn)問題都會導(dǎo)致鼓泡。引起結(jié)合力不好的原因有很多,經(jīng)常易出現(xiàn)問題的是除油過程和粗化過程。除油不徹底,會引起掉皮、脫落。燈罩采用的是化學(xué)除油(塑料件不適宜用有機(jī)溶劑除油),操作時(shí),溫度升高到65~70℃,不斷地抖動工件,直到水洗后不掛水珠為止。粗化是ABS塑料電鍍中很重要的過程。粗化不足,結(jié)合力下降;粗化過度,又會使孔變大變形,結(jié)合力也會降低。由于敏化液中二價(jià)錫極不穩(wěn)定,所以敏化液易失效,如不調(diào)整,會導(dǎo)致活化失敗?;罨蛔?,會使化學(xué)鍍層沉積不全;而活化過度,使活性金屬在表面還原過多而形成不連續(xù)膜層,也會使結(jié)合力下降。我們從除油開始,嚴(yán)格按除油液配方和操作條件,又檢查粗化工序的時(shí)間、溫度,新配制了敏化液和活化液,結(jié)果化學(xué)鍍銅后仍出現(xiàn)氣泡。幾次反復(fù)試驗(yàn),結(jié)果一樣,最后斷定鼓泡不是由除油、粗化、敏化、活化引起的。此時(shí)懷疑是否料的成分及成型工藝有問題,因?yàn)锳BS塑料的成分及成型工藝與電鍍有直接的關(guān)系。ABS顆粒易吸水,要求壓注前水份含量低于0.1%,必須在80℃熱風(fēng)干燥箱中烘干2~4h,周圍環(huán)境也必須干燥。ABS塑料中不能混入其它成分。我們通過調(diào)查發(fā)現(xiàn)注塑廠將大量成型的ABS塑料件堆放在潮濕的庫房地面上,而且注塑前的原料未經(jīng)烘干。在我們的指導(dǎo)下,將要注塑的原料在80℃下烘干2~4h,經(jīng)檢驗(yàn)符合電鍍要求后再進(jìn)行注塑。改進(jìn)后的燈罩電鍍后鼓泡問題再沒有出現(xiàn)。
成型工藝注塑制件由于成型工藝特點(diǎn)不可避免地存在內(nèi)應(yīng)力,但工藝條件控制得當(dāng)就會使塑件內(nèi)應(yīng)力降低到最小程度,能夠保證制件的正常使用。相反,如工藝控制不當(dāng),就會使制件存在很大的內(nèi)應(yīng)力,不僅使制件強(qiáng)度性能下降,而且在儲存和使用過程中出現(xiàn)翹曲變形甚至開裂,從而造成鍍層的開裂,甚至脫落。所以工藝參數(shù)的控制應(yīng)使制件內(nèi)應(yīng)力盡可能小。要控制的工藝條件有原材料干燥、模具溫度、加工溫度、注射速度、注射時(shí)間、注射壓力、保壓壓力、保壓時(shí)間、冷卻時(shí)間等。
塑型后處理由于注塑條件、注射機(jī)選擇、制件造型設(shè)計(jì)及模具設(shè)計(jì)的原因,都會使塑件在不同部位不同程度地存在內(nèi)應(yīng)力,它會造成局部粗化不足,使活化和金屬化困難,最終造成金屬化層不耐碰撞和結(jié)合力下降。試驗(yàn)表明,熱處理和用整面劑處理都可有效地降低和消除塑件內(nèi)應(yīng)力,使鍍層結(jié)合力提高20~60%。
此外,成型后的塑件應(yīng)專門包裝、隔離,嚴(yán)禁碰傷、劃傷表面,以免影響電鍍外觀。檢驗(yàn)時(shí)檢驗(yàn)員應(yīng)戴脫脂手套,防止污染鍍件表面,影響鍍層結(jié)合力。